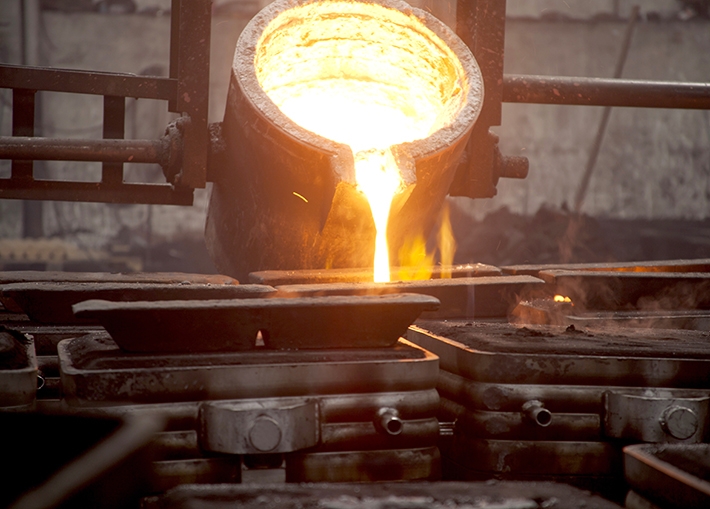
Standards for the recycling of copper have steadily gained momentum in recent years. Now, an ASTM subcommittee is ready to publish its first-ever copper recycling standard, with more on the way.
By Kathy Hunt
Jan 03, 2022
For over 10,000 years, humankind has employed copper in everything from tools to ornamentation. Archeological evidence indicates that ancient Egyptians mined and cast copper for agricultural equipment, cookware, water vessels, and cosmetics, while pre-Columbian South Americans hammered and smelted it to produce decorative and religious objects.
In the 19th century, around North America’s Great Lakes, explorers uncovered copper mines and artifacts, including knives and axes dating back 8,500 years. This strong yet malleable, orangish-red mineral has had a profound impact on history; it effectuated the end of one historic period, the Stone Age, and ushered in the next, the Bronze Age.
Thousands of years later, copper remains indispensable. According to the U.S. Geological Survey, copper ranks third, directly behind iron and aluminum, as the most frequently used industrial metal. Its ductility, thermal and electrical conductivity, and resistance to corrosion all contribute to its desirability. So, too, does its ability to be recycled repeatedly without any loss to quality or performance.
READ MORE: Standards Help Transition Economies
The International Copper Association noted that from 2006 to 2015, global manufacturers used 25 million tonnes of copper, 35% of which was recycled copper. The recycled material originated either from end-of-life products (old scrap) or from production and downstream manufacturing processes (new scrap).
A Standard Approach to Recycling
Because copper has been reclaimed for so long by so many, variations in its processing were destined to arise. Different approaches to recycling can lead to different results. Consistency, not variability, is what producers and users of recycled copper and copper alloys require.
With the need for uniformity and concerns over impurities and traceability in copper recycling increasing, ASTM International’s committee on copper and copper alloys (B05) formed the subcommittee on recycled materials (B05.08) in 2018. The 24-member group has aimed to bring copper-scrap producers — those collecting, sorting, processing, and refining this chemical element — and copper-scrap users together to create a standardized approach to copper recycling. Its standards will apply to two categories: pure copper, which is a highly refined grade of copper containing at least 99.90% of this mineral; and copper alloys such as brasses and bronzes.
“The perception is that there’s this nicely connected and coordinated value chain of copper: It’s mined. It’s refined. It’s turned into useful and sustainable products that are out there in the world for many, many decades,” says Adam Estelle, director of rod and bar at the Copper Development Association and chair of B05.08. “Ultimately, those products get collected and recycled, with the copper going around and around in this loop with no loss in material properties. In reality, the recycling sector and those producing and selling copper and copper-based alloy products are two different sectors and, at times, two different worlds. You have the scrap companies that are collecting and processing both manufacturing and end-of-life scrap with all sorts of alloy compositions, different types of product configurations, and multiple metal systems, like steel and aluminum. Then you have the companies that are purchasing scrap and remelting it to make new copper and copper alloy products like plumbing tube and brass rod. We saw an opportunity and a need to improve and strengthen the dialogue between these two sectors. And we saw how we could do that through the development of new standards.”
The subcommittee on recycled materials currently has two work items underway: obtaining a representative sample of granulated fine copper chops for the determination of physical characteristics and chemical composition (WK76562) and coding copper alloy manufactured articles for end-of-life scrap segregation (WK71320).
Estelle says that WK76562 is on track to be ASTM committee B05’s first published standard specifically related to scrap. It details a standardized method for taking a representative sample of granulated, fine copper, or copper alloy “chops” to analyze for chemical composition or other important properties. Chops are a common and very important form of scrap and are typically produced by chopping copper wires into small, uniform pieces. These pieces are used in plating and metallurgical applications and appear in automotive parts, hardware, electrical, plumbing and marine materials, fasteners, and other products.
“Although scrap producers and users typically have their own internal sampling techniques, to our knowledge, this would be the first standard of its kind to establish a consistent and harmonized method for producing a representative sample of chops for further analysis. The value of such a standard is the potential to mitigate or avoid disputes between buyers and sellers of copper chops over issues such as chemistry, metal yield, and moisture content. We anticipate the draft standard coming to ballot in the near future,” Estelle says.
Jeff Fisher of Northeast Metal Traders sees the benefit of a standardized approach to sampling. Northeast Metal Traders is a processor and broker of all grades of nonferrous scrap for customers worldwide.
“As long as both the producer and the consumer use the same method of collecting and testing the samples, we can expect to have similar results,” he says. “The system that Northeast Metal uses is designed to ensure representation of the entire scrap package, but you can find someone who just takes a hand sample off the top of the box, which doesn’t really show what the true material is from top to bottom. We want the sampling part and the testing part to be as uniform as possible. A standard process for both the supplier and consumer side will allow everyone to make a product that’s acceptable.”
More than half of the copper ever mined is still in use.
As Fisher points out, there are numerous approaches to sampling copper chops. This variety can complicate the discussion about, and selection of, one specific method.
“There are a number of processes out there that seem viable as the basis for a common practice,” says Stephen Christiansen, process engineer at Revere Copper Products and B05.08 member. “European committee members may lay their entire truckload of chop out on the shop floor and take many different samples from it. Revere’s practice, although with limited manning, is to use a sample splitter to recover 40 to 50 pounds of chop. From there, we do additional quartering to obtain a representative sample.”
Establishing a Common Language
Similar to the assortment of sampling practices for copper chop, there is an array of methods for coding copper-alloy compositions in the scrap stream. With coding copper alloy manufactured articles for end-of-life scrap segregation (WK71320), the subcommittee is focusing on a standardized coding or marking system for specific categories of manufactured copper-alloy products. This work item emulates the practice for coding plastic manufactured articles for resin identification (D7611/D7611M) from ASTM’s subcommittee on recycled plastics (D20.95). As is the custom with plastic bottles, the copper-coding system would include visual identifiers. These would aid scrap-processing facilities, scrap dealers, smelters, ingot makers, brass mills, and other recycling stakeholders in distinguishing and segregating end-of-life scrap.
“Every company that deals with this already has their own work instructions on how to identify their scrap materials, whether they’re returning them to a remelter or selling or remelting the materials themselves,” says Eric Boes, senior corporate quality engineer at Delta Faucet Company. Boes is also a member of the recycled materials subcommittee. “As is often the case, it becomes advantageous for everyone to talk the same language and have a commodity identification that puts everyone on the same page. That’s what we’re trying to do with this work item.”
The increasing number of copper alloys necessitates the use of this common language. It also spurs the need for a consistent way to identify material composition.
“In the old days, we had eight or nine core alloys. Now we’re looking at 40 to 50 alloys and, as a result, when we go to recycle, there’s an even greater risk of contamination,” says Larry Wojnicz, principal materials engineer at the consumer electronics company Molex and member of B05.
At Molex, copper alloys are carefully segregated, with scrap separated into different containers based on alloy.
“If you’re making hundreds of products and you have all these different alloys, you will have hundreds of different scrap boxes, enough to fill a whole warehouse. At Molex, we’ve come up with combinations of scrap numbers and what scrap numbers are compatible with other scrap numbers. We segregate, but we also consolidate,” Wojnicz says.
Regarding the consolidation of scrap, he says the producer and user must work together to understand the compatibility of materials and impurity levels. If the wrong scrap gets mixed together, processing will go awry.
As more alloy compositions are developed for different applications, the opportunity for scrap contamination increases. One reason for this elevated risk is that some alloys are identical in physical appearance. Yet, due to the presence of different alloying elements, they are not identical and should not be recycled together in certain situations.
“Depending on the product and process, not all the alloy families play nicely with each other in the recycling stream,” Estelle says.
If undetected contaminant sneaks into a remelted feedstock, it can result in a number of costly issues such as off-spec melts, processing failures, and degraded material properties. It could affect the material properties of the product and force the user to start from scratch. These impacts can be very expensive to remediate and can damage the relationship between the producer and the user.
FOR YOU: Radiography Moves Into the Future
“Impurities have become more difficult to detect, with traceability significant, too, especially as we see more impurities contained in the copper slipping through the scrap stream. Having that traceability to find out where the impurities are coming from and how to control them would be very helpful,” Christiansen says.
Bring Producers and Users Together
In order for new recycled copper and copper alloys standards to succeed, producers and users must provide input. Only then will the standards be able to address the requirements of both parties.
“We are at a point where, in order for us to be successful and develop documents that are meaningful and that create value in the marketplace, we have to have all parties at the table. We want these documents to be vetted by folks who are operating in that recycling sector. That includes members of ISRI [Institute of Scrap Recycling Industries],” Christiansen says.
A worldwide, U.S.-based, nonprofit trade association, ISRI advocates for safety and responsibility in scrap recycling. Among other things, it provides guidelines and defines grades for scrap packages, including copper and copper alloys.
“The standards we are working on are intended to complement, not compete with, existing standards developed by ISR and other organizations. In fact, we have opened a productive dialogue with ISRI and are very fortunate to have some ISRI members at the table to ensure that any standards we create are reasonable, practical, and create value for both producers and users of copper-bearing scrap,” Estelle says.
For more information about or to become involved with ASTM International’s recycled copper and copper alloy subcommittee, please contact Adam Estelle at Adam.Estelle@copperalliance.us. ■
Kathy Hunt is a U.S. East Coast based journalist and author.
January / February 2022