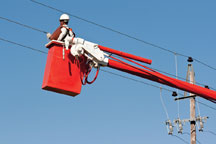
Working Out on a Limb
Acoustic Emission Inspection Standards for Aerial Personnel Devices
Acoustic emission provides a practical way to check the integrity of bucket trucks. Standards from ASTM International Committee F18 on Electrical Protective Equipment for Workers provide the test methods.
When doing your job requires being in a fiberglass bucket on a boom that stretches from 45 to 150 feet (14 to 45 m) or more into the air, safety is paramount. That's the case for utility workers who maintain the distribution and transmission lines strung between the poles and soaring towers of the nation's power grid. Any serious undetected defects in aerial personnel devices - also known as bucket trucks - from the pedestal of the boom to the bucket, could have catastrophic results.
"Typically, defects are due to overloading, abuse or improper maintenance of the bucket truck, usually the latter," says Jerry Tanner, marketing manager for Diversified Inspections/ITL in Phoenix, Ariz., and a member of ASTM International Committee F18 on Electrical Protective Equipment for Workers. Bucket truck owners and operators are expected to do a daily visual inspection as well as a periodic, or at least an annual, comprehensive inspection.
Acoustic Emission Testing
The concept of using the science of acoustic emission to evaluate the condition of fiberglass-reinforced plastic has been around since the 1970s, but employing it to check the in-service condition of bucket trucks in the utility industry began in the 1980s. AE inspection is based on the fact that materials under stress emit sound waves. When captured by the proper equipment, sound waves can be evaluated based on their strength, or amplitude, and their location within the bucket truck. Although additional methods can be used to assess the safety and soundness of other components of a bucket truck, AE is the only cost-effective nondestructive method for checking FRP components.
According to Frank Petrasek, fleet engineering manager at Atlanta-based Georgia Power Co., AE testing is designed to discover degradation of the FRP, including cracks, voids and delamination, or separation of the fiberglass and resin. Such testing can also detect cracks in metal caused by fatigue or overloading. Especially important, AE testing can alert operators to the location of cracks that are difficult to inspect visually, explains Keith McPherson, a North Carolina-based engineer with Altec Industries, and an F18 member.
Simulating Field Conditions Without Compromising Components
During an AE test, heat, load, pressure and other stressors are applied to simulate the way a device or structure is used in the field. Inspectors stress the device slightly beyond a user-designated rating that is always less than the designed maximum capability engineered by the manufacturer, but above what the device experiences in the field. Because the inspector's test load is always below the manufacturer's designed maximum load, there's no danger that the acoustic test will compromise the components of the device being tested. If inspectors find evidence of any damage or defect that might be increasing, they evaluate the amount of emissions and/or their rate of growth based on requirements in published test standards and decide whether the device or structure should remain in service, be repaired or be replaced.
Failures of aerial personnel devices can be dramatic and catastrophic for utility workers due to the heights involved. When booms fail, they can break at the pedestal or even along the shaft. Additionally, cylinders can fail, causing a boom -and its bucket - to drop.
Standards for Acoustic Emission Testing
The first test standard for field use of AE inspection of aerial personnel devices was ASTM International F914/F914M, Test Method for Acoustic Emission for Aerial Personnel Devices Without Supplemental Load Handling Attachments, originally published in 1985. The standard was developed by Subcommittee F18.55 on Inspection and Nondestructive Test Methods for Aerial Devices, which is part of F18, a committee that includes representatives of the utility industry, safety consultants, manufacturers of aerial devices and acoustic emission testing organizations. This standard was followed in 1992 by F1430/F1430M, Test Method for Acoustic Emission Testing of Insulated and Non-Insulated Aerial Personnel Devices with Supplemental Load Handling Attachments, and in 1997 by F1797/F1797M, Test Method for Acoustic Emission Testing of Insulated and Non-Insulated Digger Derricks, concerning derricks that bore holes and set posts.
In the years since the standards were published, each one has been reviewed and revised several times. In fact, AE data interpretation techniques, test equipment and field experience have evolved, and as the standards are revised at the required five-year intervals, the word insulated will be removed from the standards' titles to reflect a broader application of the AE inspection process and data interpretation techniques.
Additionally, ASTM Subcommittee F18.55 has developed acceptance/rejection criteria, which are now included in the latest revisions of the test method standards.
Discovering Defects
Using ASTM International standards for AE inspection, utilities and testing organizations have found cracks in the FRP booms of aerial personnel devices; damaged material handling jibs or winches on bucket trucks; and problems with hydraulic holding valves. Inspections have also uncovered inadequate lubrication of pins and bushings, and epoxy debonding at metal-to-FRP interfaces, resulting in repaired or replaced equipment and enhanced safety for workers.
Additionally, AE inspection has been used to inspect bucket trucks after suspected damage. For example, notes McPherson, if a bucket truck experiences an overload caused by using its winch to pick up a heavy object, AE testing can be helpful in determining whether any significant damage has been done.
Other NDT Test Methods
To ensure a thorough inspection of an aerial personnel device, ASTM International standards also encompass other nondestructive test methods that should be used in conjunction with AE, notes Tanner. These standards include ultrasonic inspection that can identify defective pins; magnetic particle inspection to uncover welding cracks; liquid penetrant testing; and dielectric testing, where high alternating or direct current voltage is used to test the integrity of FRP and ensure that it does not conduct electricity.
Benefits of Standards and Certified Inspectors
Since the first ASTM AE standard was published, AE testing has uncovered defects that might have cost lives if undetected, Tanner explains. "It has also saved money by detecting defects that, had they gone unnoticed, would have cost much more to repair." Tanner adds that having testing standards ensures consistency in testing and data collection, allowing any consultant or testing agency to get similar results.
Regardless of the inspection method used, however, inspectors should be certified and have years of experience testing and interpreting data for specific devices or structures. In fact, inspectors using ASTM standards are required to be certified under the American Society for Nondestructive Testing Recommended Practice No. SNT-TC-1A: Personnel Qualification and Certification in Nondestructive Testing.
AE testing has made great strides in its ability to locate and evaluate defects in both FRP and metal components of aerial devices for the utility industry. AE testing is now also used to detect leaks and other defects in underground piping, railroad tank cars, pressure vessels and aboveground storage tanks. In the hands of trained competent personnel, AE testing is an invaluable tool for maintaining the increasing complex inventory of equipment in utility fleets, the pulp and paper industry, power generating plants and many other industries.