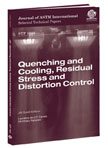
Metals Quenching
Two ASTM Publications Address Alloy Heating and Cooling
Quenching, the practice of heating and cooling metals under controlled conditions, requires an understanding of both the process and the effects it has on materials.
The quenching process most commonly requires petroleum, but air, high pressure gas, molten metals and salts, aqueous water-soluble polymers, brine solutions and water are also used. Its purpose? To form a specific microstructure, with designated hardness and/or mechanical properties. Done successfully, quenching controls distortion and any resulting stress field in the processed alloy, resulting in a longer service life.
Two recently published ASTM International books gather together information about quenching, intensive quenching and related issues to aid practitioners in the field. STP 1523, Quenching and Cooling, Residual Stress and Distortion Control, compiles 59 peer-reviewed papers on these topics into one volume. Manual 64, Intensive Quenching Systems: Engineering and Design, guides metallurgists and mechanical engineers in both designing and implementing quenching systems.
The impact of quenching on the heat treatment of nonferrous and ferrous metals forms the central theme in STP 1523, which gathers together papers that have been published in the Journal of ASTM International since 2008. Editors Lauralice de C.F. Canale, University of São Paolo, Brazil, and Michiharu Narazaki, Utsunomiya University, Japan, organized the papers into sections covering topics from heat transfer and stresses to cooling curves and dilatometric analysis. The papers on heat transfer, thermal process modeling and gas quenching hold particular significance because they update ongoing technology developments. STP 1523 treats quenching for steel and aluminum alloys, which manufacturers use for such purposes as automotive, aerospace and locomotive parts.
Manual 64 considers intensive quenching using plain water instead of oils and polymers with 13 chapters that address the factors to consider during intensive quenching system design. Co-author Nikolai Kobasko, Ph.D., says that, unlike oil quenching, which does not need an interruption to the cooling process, "Intensive quenching should be interrupted when compressive stresses reach their maximum value at the surface of steel parts or at the end of transient nucleate boiling processes." Kobasko, director of technology and R&D for IQ Technologies Inc., Akron, Ohio, and president of Intensive Technologies Ltd., Kyiv, Ukraine, wrote the book with Michael Aronov, Ph.D., CEO of IQ Technologies; Joseph Powell, president of IQ Technologies; and George Totten, Ph.D., G.E. Totten and Associates LLC, Seattle, Wash.
Kobasko notes that calculations such as heating and cooling time periods must be made to achieve desired material strength and increased service life. The work, which enables users to address potential problems, pays particular attention to replacing relatively expensive alloyed steels with less expensive carbon steels for machine parts to be used under normal operating conditions. "This important-for-the-practice issue is widely discussed in Chapter 12 of the manual," he says.
Totten, a veteran ASTM International member who works on Committee D02 on Petroleum Products and Lubricants, notes that, other than a volume published last year, the last comprehensive books on this subject were written in the early 1990s. Now, engineers, academics and students can refer to these two additional works - STP 1523 and Manual 64 - for current details about these technologies.