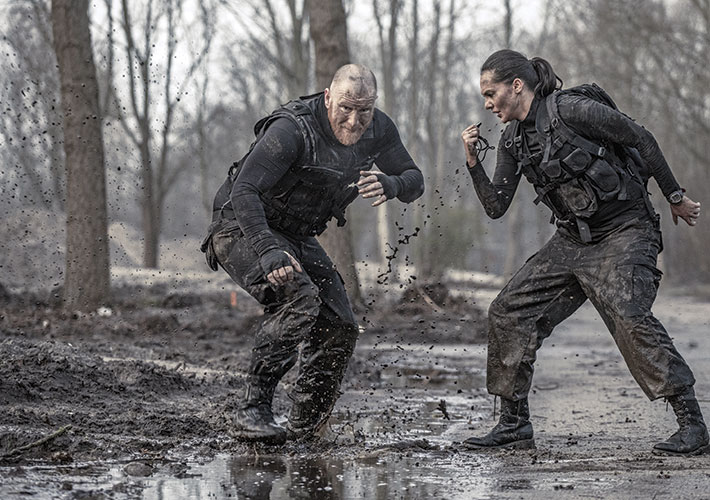
Building a Better Boot
Until recently, no matter where they were stationed, most U.S. soldiers wore the same combat boot. The footwear performed well in arid climates, such as the deserts of Iraq, but proved problematic in humid or wet environments. Once the combat boot got wet, it stayed wet, leaving the wearer with perpetually damp and sore feet. For soldiers who waded through rivers, swamps, thigh-high mud, or heavy rain, the need for a tougher, moisture-resistant boot was tremendous.
In 2017, as part of a project by the U.S. Army Project Manager — Soldier Protection and Individual Equipment, the plight of those stationed in steamy, sodden lands improved with the issuance of a jungle-ready combat boot. Released to the U.S. Army’s 25th Infantry Division in Hawaii for testing, the new boot includes holes and an insert to increase drainage, a quicker-drying lining, and speed laces for easier fastening and removal. The boot also has a foam layer that both absorbs shock and keeps out harmful microbes.
After months of field testing, the soldiers provided feedback on their boots. Critiques in hand, designers went back to their drawing boards to make further alterations
So, where do standards fit into this picture? A final step toward getting this new type of boot to the soldiers who need it will be to shift U.S. Army purchase descriptions and military specifications from material and design requirements to performance standards.
“Our hope is that transitioning away from defining specific materials and manufacturing processes will allow our industry partners to take advantage of these technologies,” says Albert Adams, lead footwear project engineer at the Natick Soldier Research, Development, and Engineering Center. “The goal for this is to eventually expand beyond jungle combat boots to all military footwear.”
Moving toward Performance Standards
To make sure this shift occurs, representatives from the U.S. National Institute of Standards and Technology, the U.S. Department of Defense, the American Association of Textile Chemists and Colorists, ASTM International, and SATRA came together with footwear industry representatives in January to discuss performance standards for footwear, including jungle combat boots. (SATRA is an independent research and testing company in Kettering, United Kingdom, and a leading technical authority on leather and footwear.)
Four working groups comprising these stakeholders are now evaluating both existing and proposed requirements. Their work could lay a foundation for improvements to other U.S. Army clothing and equipment specifications and could also become a template that could be used in other countries.
The U.S. Army Project Manager — Soldier Protection and Individual Equipment is charged with creating and enhancing soldier protection products, including comfortable uniforms and gear, according to Cassy Robinson, a physical scientist at NIST. “One method for improvement is transitioning their standards, purchase descriptions, and specifications from detailed material and design requirements to performance requirements, to the extent possible. Such a transition would allow innovation and use of new materials and technologies, and ultimately improve the comfort, protection, and performance of the boot,” says Robinson, who is vice chair of ASTM International’s committee on homeland security applications (E54).
Mike Wilson of SATRA agrees. “Moving towards performance from design requirements puts the needs of soldiers and personnel first, and it allows industry to move forward with technological innovations that will benefit the users,” says Wilson, senior footwear consultant at SATRA.
A Look at the F our Working Groups To collaborate on these jungle combat boot performance standards, four working groups have been established. Each group includes stakeholders from NIST, SATRA, AATCC, DOD, and the ASTM International committees on pedestrian/walkway safety (F13), textiles (D13), leather (D31), and personal protective clothing and equipment (F23). Their efforts could result in new standards, revisions to existing standards, and new research projects.
For example, “there are no standards for ankle support. An outcome of this work may be to propose a standard test method for ankle support,” says Bert M. Coursey, Ph.D., currently a guest researcher in NIST’s Standards Coordination Office and an ASTM International member since 2003.
Working Group 1
Biomechanics and Injury Reduction
The first working group studies issues such as ankle support and impact reduction in combat boots.
With input from specialists in sports medicine, engineering, and other biomechanics-related fields, the members are looking at boot performance in crucial areas such as plantar pressure, torque on the joints, and positional measurements. They will also determine whether upgraded testing procedures are needed and, if so, what the new methods will be.
Working Group 2
Fabrics and Leather
Concerns about leather properties and baseline performance as well as fabric testing are the focus of the working group on fabrics and leather.
“Materials currently specified for jungle combat boots include traditional footwear materials such as leather and nylon for uppers and rubber for outsoles. The expected benefit of this work is that any material that meets the performance requirements may be used, so no particular material would have to be specified,” says Jeffrey Stull, International Personnel Protection Inc., and lead for this working group.
The use of technologically advanced and better performing materials should help provide faster drying, better drained, and/or less absorbent boots, especially when used in humid and wet environments. Soggy socks and boots can cause trench foot and other podiatric problems. It could also be a boon to those who inadvertently tramp on sharp, foreign objects and puncture the soles of their boots.
Bill Ells, vice president of component sales at Vibram, is an ASTM International board and F13 member. He adds, “A number of the materials which were sourced for the current PD [purchase description] version, as well as PD version two, are newer, more technical materials. So, too, are the overall boot and product physical design changes. Given this new calibration with its broader input, more scientific approach, and focused goals, collectively, we expect to spur the potential for even greater performance.”
Working Group 3
Liquid/Vapor
The whole liquid/vapor test methods working group is addressing the matters of whole boot moisture management and breathability. This group will evaluate water absorption, drying time, and the moisture vapor transition rate (the difference in temperature and concentration of vapor inside and outside the boot, that is, breathability). The group will also be investigating how well Army footwear drains after being immersed in water.
The current U.S. Army Purchase Description method for determining moisture vapor transmission rate involves placing a hot water-filled bootie inside a test boot and assessing the evaporation level after six hours. The D31 committee has standardized the approach as the test method for whole boot breathability (D8041), and the work group will assist the committee in identifying further enhancements and improvements to the method.
Working Group 4
General Design Requirement Concerns
The fourth working group, general design requirement concerns and other issues with purchase description, is focusing on 23 general footwear requirements not addressed by the three other groups.
These include fundamentals such as boot height and weight and the designs of outer sole and midsole, which is the layer of foam between the insole and outsole or tread. Construction requirements, such as drainage holes and whether the sole is attached through injection molding or open pouring also fall into this category.
Next Steps
By July, the four working groups aim to make their recommendations for jungle combat boots standards. They have until September 30 to create and implement R&D plans for their respective areas — biomechanics and injury reduction, fabric and leather, liquid/vapor test methods, and general design requirements.
If the entire process goes smoothly, NIST hopes to recreate it for other U.S. Army gear and equipment. Once the work on jungle combat boots has finished, the next topic for performance standards would be lightweight, flame-resistant head and neck protection.
Kathy Hunt is a U.S. East Coast-based journalist and author.